Project footprint: about 17,000 ㎡ Storage locations: 17,000+ This project is in Changzhou. The customer is a leader in the world's lithium-ion battery separator industry. To develop its services, it needed to build an automated storage and retrieval system (AS/RS) for efficient inbound and outbound management of lithium-ion battery separator products. The customer's pain points include large inbound and outbound flows, insufficient automation level, and insufficient information level. Based on this, Wayzim introduced a Stacker Crane Multi-level AS/RS.
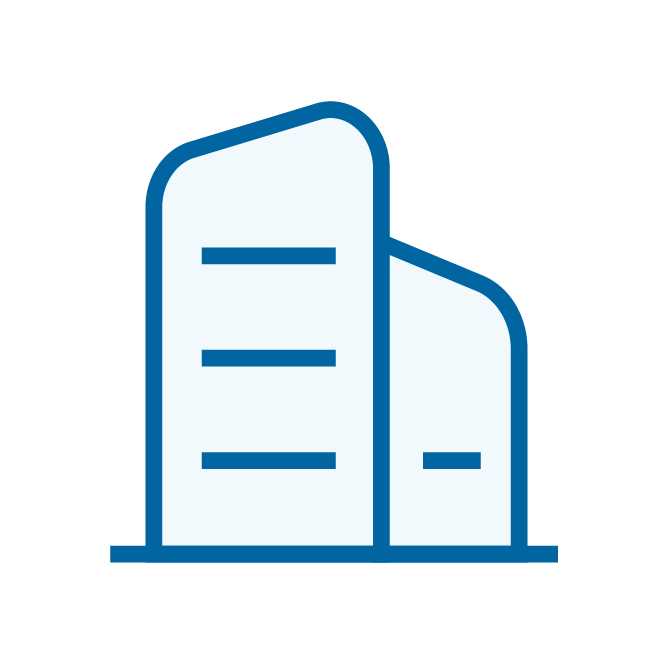
Project footprint
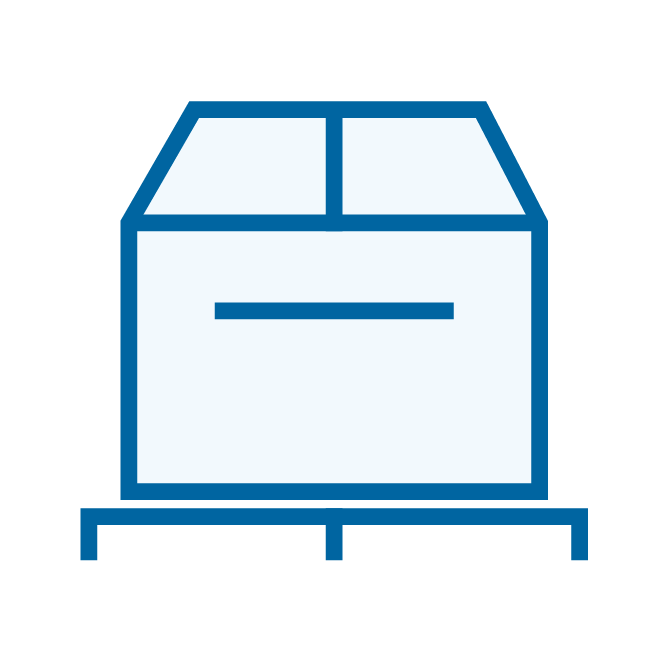
Storage locations
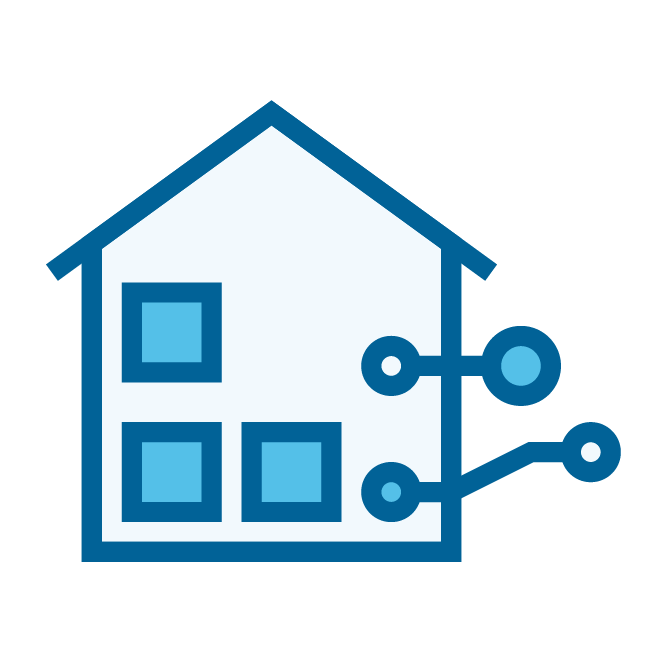
Comprehensive inbound-outbound circulation efficiency
With the growth of market demand and the continuous improvement of customer business, the storage demand for lithium-ion battery separator products has increased sharply. Insufficient storage locations lead to product accumulation, affecting inventory turnover rate and supply chain efficiency.
Manual operations involve a lot of manual handling and recording, which are slow and error-prone, and cannot meet the requirements of efficient operations. At the same time, due to the lack of advanced automation systems and data management tools, it is difficult to achieve fine management and real-time monitoring of the cargo circulation process, which affects the overall operational efficiency.
To fully meet the customer’s needs, Wayzim deployed multiple Double-reach Pallet Stacker Cranes and automated conveying lines and used both a warehouse management system (WMS) and warehouse control system (WCS) for unified scheduling to create an automated and intelligent Stacker Crane Multi-level AS/RS.
Pallets carry materials to perform automated turnover operations in the conveying lines and automated warehouses, significantly improving the storage density and inbound and outbound efficiency while greatly reducing the operating costs of the enterprise. After the project has been successfully implemented, the material transportation between different factory buildings and storage areas achieves a dynamic balance, and the warehousing system can flexibly adapt to and promptly respond to various storage and transportation needs.
An AS/RS is deployed with stacker cranes as the core based on the actual height of the warehouse, making full use of the vertical space. Materials are transferred among storage areas in one factory building through conveyor lines in front of shelves, and transferred among factory buildings through vertical reciprocating conveyors. This ensures that the warehousing system can flexibly adapt to and promptly respond to transportation needs.
A high-precision 3D model of the warehouse for 3D visual effects allows the customer to monitor and manage automated equipment in an all-round way. When the equipment breaks down, the model can help the customer quickly locate the problem and provide fault information, thus reducing downtime and improving the operation efficiency and reliability of the overall warehousing operation.